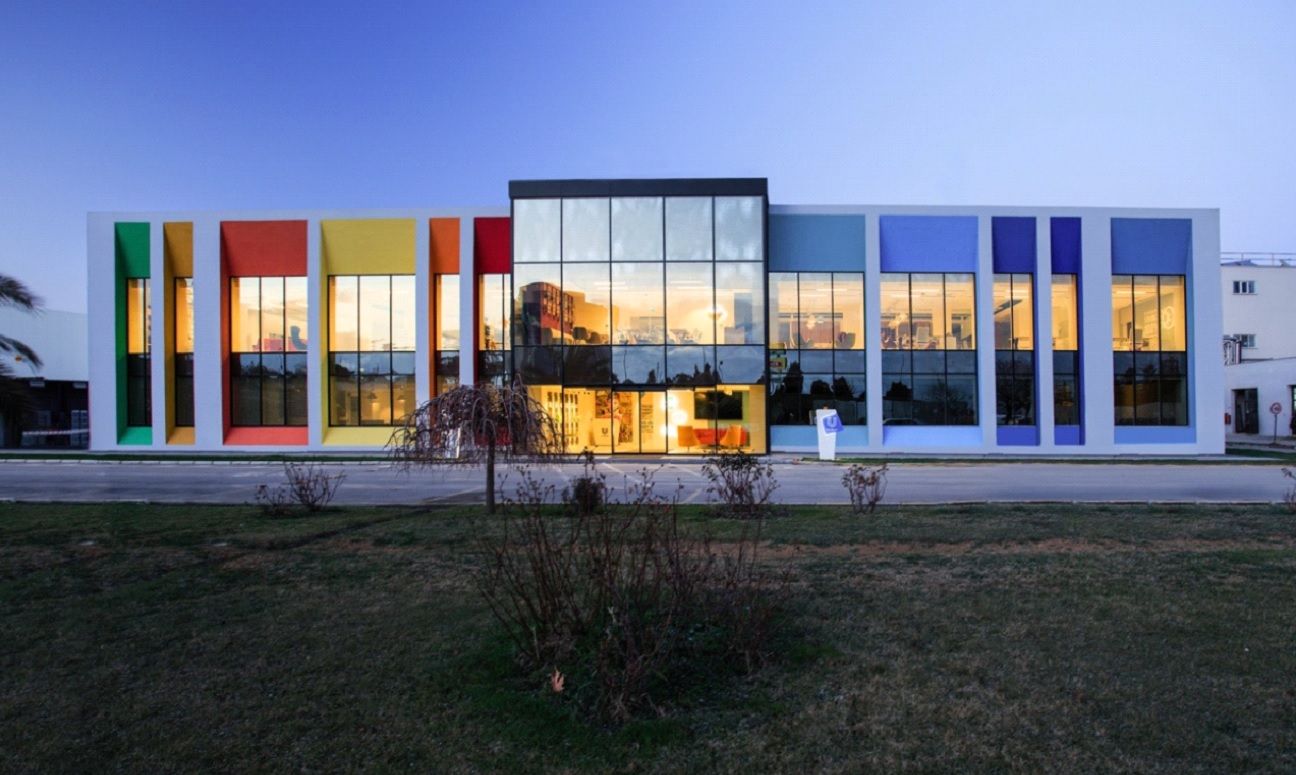
Unilever
Boosting Productivity at Unilever Besan
With this solution, the UNILEVER BESAN factory can utilize its space to the fullest capacity. Robots allow for perfect traffıc management as they move seamlessly within the existing facility with no added infrastructure. Automating the transfer of materials between operations greatly improves effıciency. Human workers are able to give their ful/ time and effort to ski/1-needed operations, thus reducing labor costs.
Unilever Besan
Unilever is one of the world's largest companies. With over 400 brands, Unilever manufactures and distributes homecare, personal care, food, and drinks to over 2.5 billion people worldwide.
The UNILEVER BESAN factory produces a high volume of food and beverage products to be distributed throughout Turkey and exported to the European and Asian markets.
- 5.000+ Employees
- 20.000 m² Production Area
The Challenges
Challenges in Material Flow Inefficiencies
This facility utilized multi-point conveyor inputs and outputs as well as multi-point to multi-point material distribution, resulting in complex and intersecting paths between key locations. There were no dedicated paths or directions. A traditional conveyor system would be nearly impossible with the existing setup, as it would need intersecting static conveyor lines, which would be costly, complex, and would create roadblocks in key areas.
Despite the tight space, forklifts, human workers, and AMRs were working in the same area on multiple operations at the same time, creating traffic jams and unsafe situations for workers. With three shifts and 24/7 operation at high outputs, labor costs were high. These high labor costs were exacerbated further by the fact that operators who could have been used in a skill-needed duty were spending time carrying materials between locations.
In some cases, unstretched materials needed to be carried on pallets, causing safety and stability concerns. Production, stretching, and truck loading were ali automated. However, the operator-dependent transfer of materials between operations was slowing things down, preventing a fully-automatic trackable operation flow. Different truck destinations matched with different material types based on the orders. However, this facility did not have full integration with the EOL output MES, truck schedule system or AMR fleet management system.
Additionally, there was a need for greater speed and efficiency overall, particularly during peak season. Pallet delivery needs doubled during peak season from 60 pallets per hour on average to approximately 120 pallets per hour at peak.
The Solution
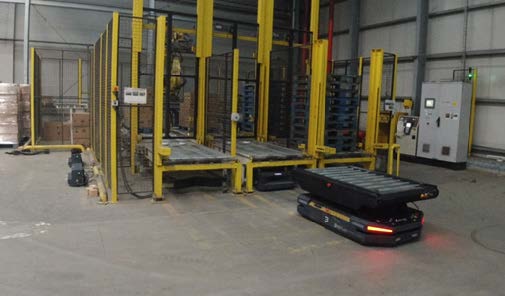
Implementing Mobile Conveyor AMRs
To solve UNILEVER BESAN's logistics problems, our main aim was to connect multi-point conveyor inputs and outputs with a flexible solution by converting our robots into mobile conveyors rather than using intersecting, area blocking, high-cost static conveyor lines. This included providing automated intralogistics operations to complete end of line automation via an automatic palletizer with empty pallet stack feeding, an automated stretcher and automatic truck loading.
Customizing the Robots
To solve the stability issue with carrying unstretched materials, robots are programmed for more attentive movement when carrying materials that have not yet been stretch-wrapped.
Integration and Deployment
Operations are now fully integrated. After palletizing, robots can transfer unstretched material to the next available stretching machine without human intervention. Additionally, they can automatically feed empty pallets into the palletizers when needed. After the pallets are stretch-wrapped, they can transfer end products to the trucks by checking truckload availabilities so as to fili each truck to the maximum capacity without any human intervention.
“Working with the Milvus Robotics team was a very straightforward process and it is clear that they are dedicated to their work. From their wide selection of robots and attachments, they selected those that would be most cost-effective and efficient for us in the long run. it was clear that a mobile conveyor system (based on AMRs) would be much better suited to our facility than an overly complex static conveyor solution. We were very impressed with their detailed engineering study and their overall approach to the project. Now, traffic flow is greatly improved, safety has increased, and it is overall more systematic and productive.”
Operation Manager, Unilever BESAN
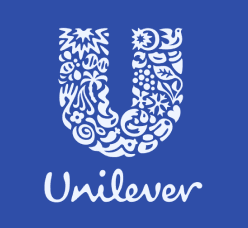
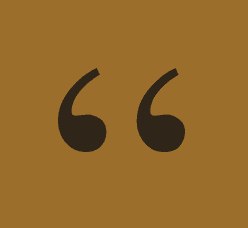
The Results
With this solution, the UNILEVER BESAN factory can utilize its space to the fullest capacity. Robots allow for perfect traffıc management as they move seamlessly within the existing facility with no added infrastructure. Automating the transfer of materials between operations greatly improves effıciency. Human workers are able to give their ful/ time and effort to ski/1-needed operations, thus reducing labor costs.
Unilever Konya HPC Factory
Lorem ipsum dolor sit amet.
One of the most appealing features of AMRs is their ability to complete various different tasks and navigate virtually any environment. They are flexible and adaptable.